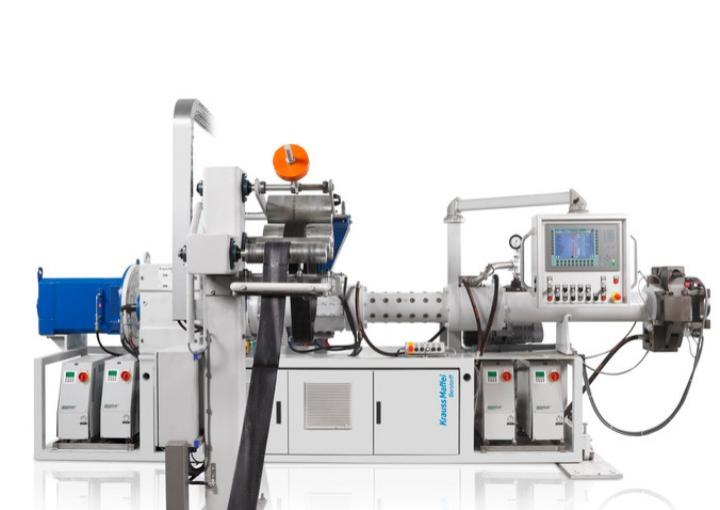
COLD-FEED GE-K RUBBER EXTRUDER
The cold-feed rubber extruders from the GE-K series are the ideal machines for simple treatment processes. It only requires a little space in order to show its strengths due to its compact design. Its high degree of automation makes it an easy-to-operate machine. The GE-K series offers high production reliability thanks to high product quality, established reliability and high recoverability.
The GE-K series is designed to be plug-and-go, so that it can be commissioned quickly. The robust gearbox and optimally-sized drive designs with a water-cooled AC motor provide long service life and low maintenance costs.
The vacuum systems on Vac GE-K extruders are individually matched to the process. The machines provide high outputs, low melt temperatures downstream of the injection mold and even better size stability for the extruded products.
COLD-FEED PIN-BARREL RUBBER EXTRUDER GE-KS
GE-KS and Vac GE-KS pin-barrel rubber extruders are all-around machines for a wide variety of applications. Their flexibility and reliability make them true success machines in the treatment process. The attractiveness of pin-barrel extruders is enhanced even further by the expansive suite of series equipment, such as an automatic pin adjusting device, replaceable wet sleeves, a pin breakage display and high-performance screws.
The advanced technology processes a wide spectrum of rubber compounds of varying viscosity with just one screw type without requiring a conversion.
We equip Vac GE-KS degassing extruders with a vacuum zone and a procedure part utilizing pin-barrel technology. The machines provide high outputs, low melt temperatures downstream of the injection mold and even better size stability for the extruded products.
COLD-FEED PINCONVERT® GE-SC EXTRUDERS
A defining feature of the KraussMaffei Berstorff GE-SC Pinconvert® extruder is a throttle element built into the area near the maximum channel volume of the sleeve.
It has pins distributed symmetrically around the circumference that radially penetrate into the channels of the barrel sleeve. These can be adjusted manually or electrohydraulically and allow the channel volume to be reduced to zero in this area.
Because this allows the output, melt temperature and homogeneity performance parameters to be influenced and optimized, GE-SC extruders provide you with a guarantee for flexibility and adaptability that cannot be beaten.
We expanded the implementation options for our GE-SC Pinconvert® extruder using a specially developed cylinder degassing system. The throttle element is of critical importance for these extruder versions as well, since the extruded material filling level can be influenced using the pin penetration depth before it reaches the degassing zone.